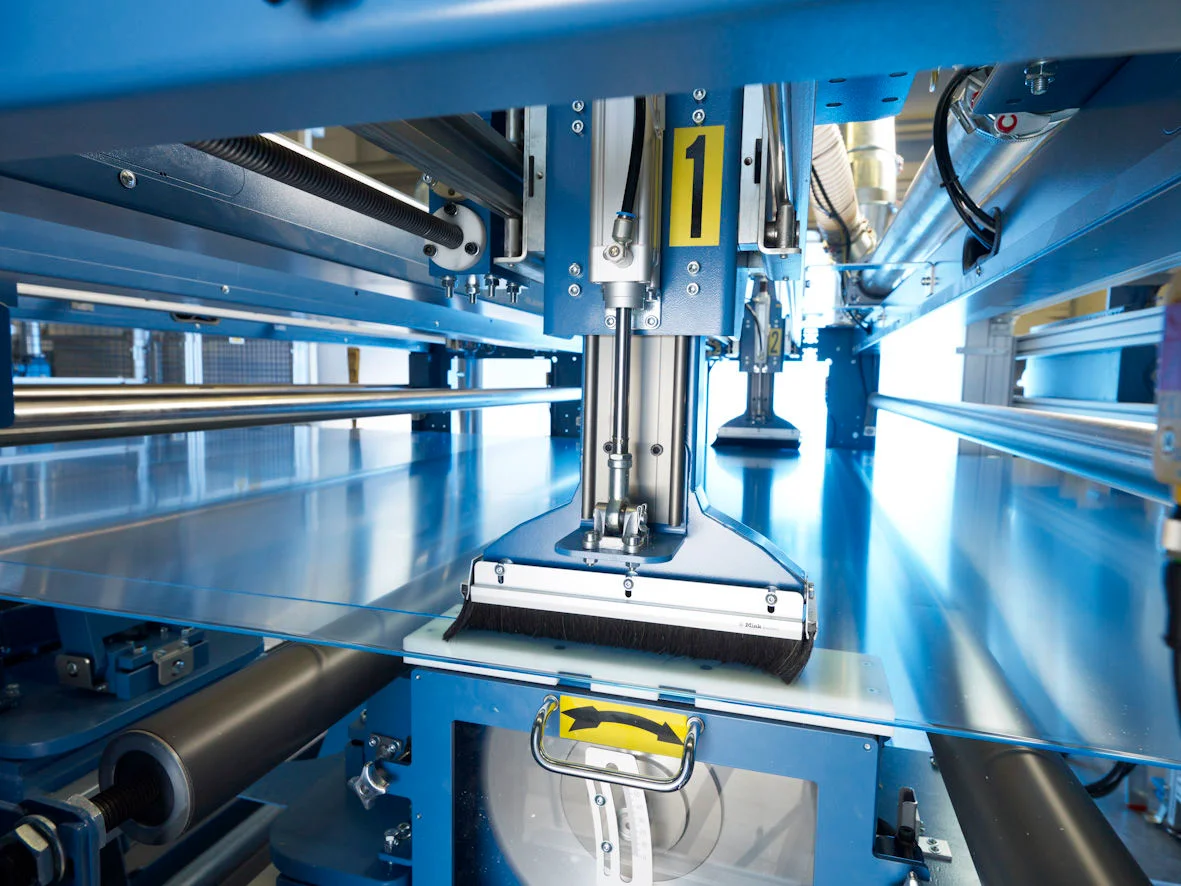
Product Center
Coating Die Series
Hollow lattice plate die series
amination Film Die Series
Sheet Die Series
Cast Film Die Series
Coating Die Series
Sheet Die Series
Multi-layer co-extrusion Lamination feed block
In-mold multi-layer coextrusion
Rack Plate For Extrusion Machinery
Melt metering pump
Quick screen changer
Mesh free filter
Perovskite coating series
Hot melt adhesive coating series
Photoresist (lithium battery coating series)
Scraper (slit, comma) series
Adhesive coated die head series
Automatic Die Head - Rainbow Film
Coating Die Series
Perovskite coating series
Product Description
As a new type of photovoltaic cell, perovskite has significant advantages such as high conversion efficiency, low manufacturing cost, wide application range, and strong growth certainty, and is known as the most potential next generation photovoltaic technology.
Slit coating is a common technique for preparing perovskite solar cells, and its advantages include high efficiency, low cost, and easy mass production. Slit coating technology has become a very important process in the manufacture of organic solar cells because of its high precision and high efficiency film forming characteristics.
Because of the high precision characteristics of the coating range and shape, the slit coating technology can fine-adjust the shape and contact between the components of the organic solar cell, thereby improving the efficiency of energy transfer. Compared with the traditional organic solar cell manufacturing process, the use of slit coating technology can greatly improve the photoelectric conversion efficiency and stability of the device.
In the entire coating process, the role of the coating head is crucial, which directly affects whether the coating solution can evenly cover the substrate, and whether the film thickness is uniform and neat, so the inside of the coating head and the bottom piece need to be very smooth and flawless, and a little flaw is fatal to the product.
Perovskite its high light energy conversion efficiency has been widely used in the manufacturing of solar panels, in the manufacturing process of solar panels, perovskite coating is a very important part.
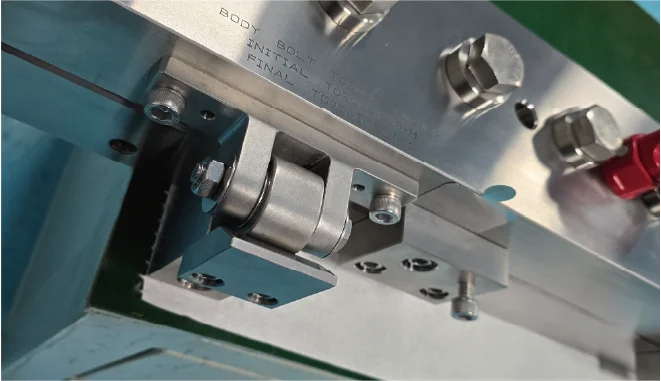
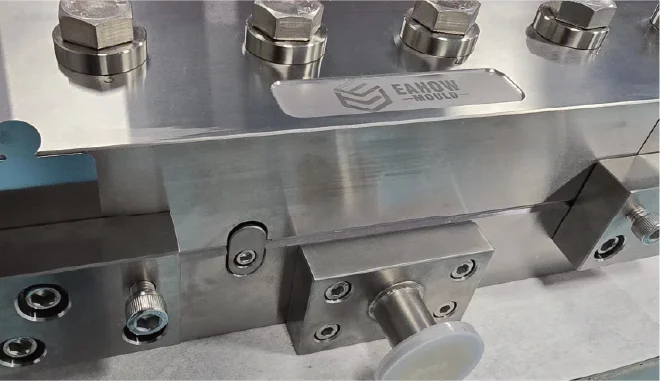
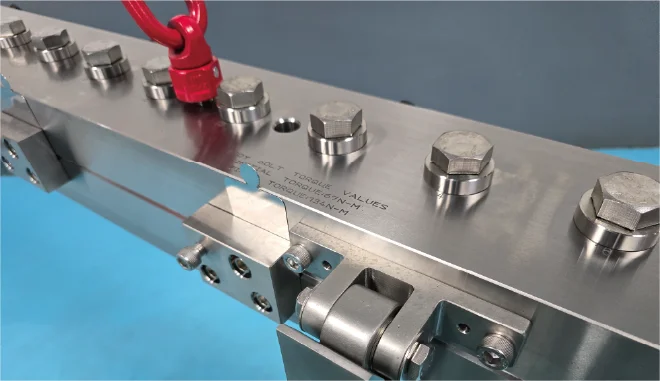
Hot melt adhesive coating series
Product Description
The hot melt adhesive coating machine is based on the properties of hot melt adhesives. The solid hot melt adhesive is heated and then evenly coated on the surface of the substrate by a special hot melt adhesive coating die. Hot melt adhesive is a polymer that is solid at room temperature, does not require solvent, does not contain water, and will melt at a specific temperature. When the temperature reaches its melting point, the hot melt adhesive will become a liquid that can flow and has a certain viscosity, so that it can be coated on the surface of various substrates.
The coating head is the key component for evenly coating the hot melt adhesive on the surface of the substrate. The coating head is usually made of metal and its inner surface is precisely machined to ensure uniformity and stability of the coating.
The application of hot melt adhesive coating is very wide, including but not limited to packaging industry, coating composite industry, cosmetics industry, automotive industry, home furniture industry, electronic assembly industry, express bag industry, medical and health industry.
Photoresist (lithium battery coating series)
Product Description
Photoresist is a key semiconductor material, in which photosensitive dry film is the core category of photoresist.
The photosensitive dry film is made by evenly coating the pre-prepared photoresist on polyester film (PET film) by a precision coating machine in a highly clean environment. After drying, cooling, and then coated with a layer of polyethylene film (PE film), and finally rolled into a film type photoresist.
Photosensitive dry film is the core raw material in PCB (printed circuit board) manufacturing, which has a direct impact on processing accuracy.
Photosensitive dry film is generally composed of three layers: polyethylene film (PE), photoresist film (sensitive layer) and polyester film (PET).
The polyester film is the carrier of the photosensitive material, which is used to assist the photosensitive material to evenly coat and form a film.
Photosensitive dry film plays a key role in the production of PCB boards in aerospace science and technology, computers, medical equipment, consumer electronics, automotive electronics and other fields.
Scraper (slit, comma) series
Product Description
Slit blade coater is a laboratory coating equipment, often used to apply a thin film coating on the surface of the substrate. During the coating process, the paint or adhesive is passed through a slit and then evenly scraped off by a scraper, so that the paint forms a uniform film on the substrate. The coating machine can accurately control the coating thickness and is suitable for the preparation and research of various film materials.
Slit scraper coater is widely used in printing, packaging, painting and other fields for uniform coating of various liquid materials, with slit scraper structure to control coating thickness. Selection points include coating speed, material compatibility, uniformity, control accuracy, cleaning and maintenance, and production capacity to meet the needs of different processes.
Comma scrapers are often made of round steel with good strength and hardness. The scraper is fixed and does not rotate when scraping. The strength and hardness of the scraper are high, the straightness error of the cutting edge is small, and the position of the scraper can be adjusted and controlled by pneumatic and fine-tuning mechanism, and the coating amount control and scraping accuracy are high, and the use is also extremely convenient. Because of its uniform scraping, it is suitable for precise scraping on smooth roller coating.
This coating method is widely used in a variety of coating lines, which is characterized by high coating accuracy, large adjustable range of coating thickness, good adaptability to glue viscosity and solid content, simple structure and simple operation.
Adhesive coated die head series
Product Description
Slit coating die head coating improves accuracy and uniformity. Slit coating technology is an advanced predictive coating technology, which can obtain a high precision coating.
Adhesive coating has wide application range, simple structure, low cost, intermittent coating, continuous coating.
Coating die heads can process various types of adhesives (including special transparent adhesives), batteries, ceramic capacitors, decorative surfaces, electronic display media, filter membranes, floors, fuel cells, magnetic mud, products, photoresist materials, pressure sensitive tapes, solar cells, superconductors, tear tape and window films.